Thursday, January 9, 2025
Eurovetrocap improves its Parigi dropper concept
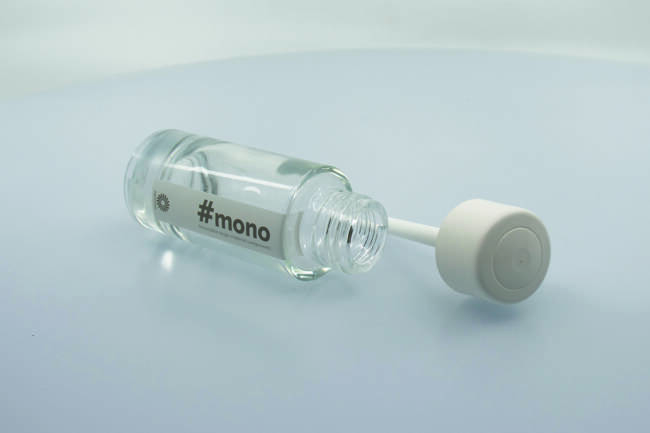
Introduce your company in a few words…
In 2020 Eurovetrocap launched Zero In•Pack, an innovative start-up within the group, which is dedicated to reducing the environmental impact of cosmetic packaging, by means of a customized LCA tool. Thanks to the training of the team and a real concern about environmental issues. Zero In•Pack is able to offer a technical and scientific support to the customers and sales team. The start-up also helps guide the product development, in order to avoid any form of rebound effect or impact transfer. This process is targeted with a strong emphasis on recycled materials, mono-material items and impact reduction at all stages of the life cycle of packaging solutions. The combination of a quantified approach to environmental impact and technical expertise thus offers to all brands the guarantee of an optimized packaging solution at all levels.
Last year, you presented Parigi dropper. How brands reacted to this packaging?
We had an overall positive response from brands of diverse market segments. We knew when we first presented this innovation that it might not be to the liking of everyone. In particular older generations and luxury brands still have a very traditional approach of what beauty packaging, and especially droppers, should look and feel like. That is the reason why we primarily targeted indie and natural brands. We did not expect such a level of interest! We have a couple of customers eager to launch new lower-impact products with it, and they are waiting for the final version!
Any changes or innovations to report on this product?
The prototype we presented last year helped us test the waters and receive feedback from potential users to improve the concept. Aesthetically, little change was brought about, namely the elimination of a contrasting shiny ring on the cap’s bottom and the design of a clearer pressing area. Production wise, we opted for a bi-injection process and mold, which allowed us to reduce the share of flexible material in the upper part of the cap and to improve the user experience thanks to a softer push button, as well as increasing once again the level of recyclability of the dropper through existing PP waste streams.